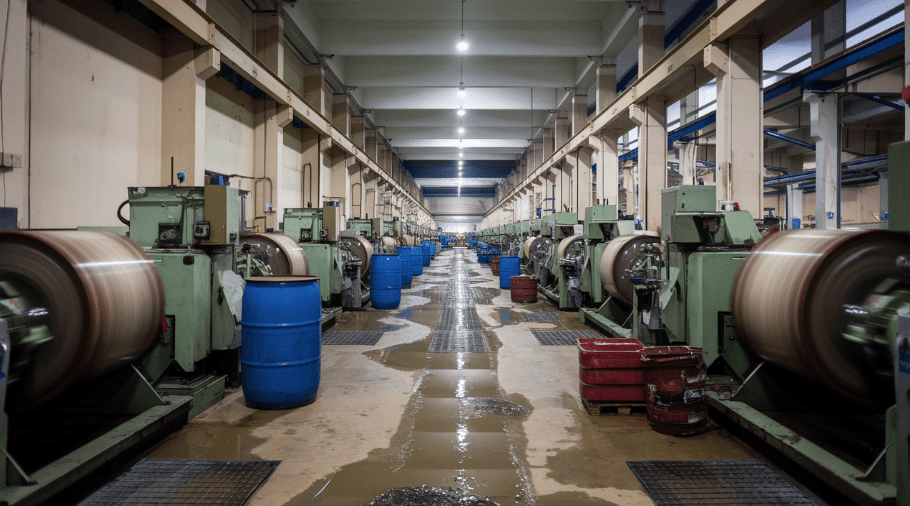
Improving Fire Safety in UK Factories: Compliance & Best Practices
One of the biggest threats to businesses in the UK is the threat of fire, this stands especially true for factories. The potential damage to high-end machinery and a high stock inventory can easily run into the millions as a result of a fire.
Everyday, factories across the UK are required to go “All-in” on their fire safety measure to keep compliant with the Regulatory Reform (Fire Safety) Order 2005.
In the year ending March 2024, there were 1,774 fires in industrial premises across England. These incidents not only endanger lives but also result in substantial financial losses in machinery and equipment.
Staff, machinery, property and stock are at the forefront of any business owners protection list, and compliance with the Regulatory Reform (Fire Safety) Order 2005 keeps them on the correct side of the law.
Factory owners and building managers also need to assess the culture within your workplace. The way you communicate safety practices can make a big difference in how prepared your team is.
Are you doing your fair share when it comes to protecting your business and personnel?
Let’s explore how you can create a proactive safety environment and the best practices for factory fire safety in the UK
UK Fire Safety Compliance for Factories
Factory owners and managers across the UK must comply with the Regulatory Reform (Fire Safety) Order 2005. This legislation places the responsibility on the Responsible Person (typically the employer, owner, or building manager) to carry out fire risk assessments, implement safety measures, and ensure staff are trained.
The Health and Safety Executive (HSE) and local Fire and Rescue Services enforce these laws, conducting inspections and issuing enforcement notices for non-compliance.
Key legal requirements for UK factories include:
— Appointing a Fire Marshal (or multiple, depending on factory size).
— Providing clear fire escape routes and ensuring fire doors are never blocked.
— Installing appropriate fire detection and alarm systems.
— Keeping detailed fire safety records for inspections.
— Failure to comply can result in fines or even prosecution, especially if negligence leads to a fire.
In the year ending March 2024, Fire and Rescue Services conducted 49,835 fire safety audits in non-domestic premises, with only 58% resulting in a satisfactory outcome.
This underscores the critical need for factories to adhere strictly to fire safety regulations to avoid enforcement actions and potential penalties.
You may also like Who is responsible for fire safety in the workplace
Common Fire Hazards in UK Factories
Factory fires often start due to electrical faults, such as overloaded circuits, faulty wiring, or overheating machinery. Without regular inspections, small issues can escalate quickly. Flammable materials, including chemicals, solvents, and combustible dust, also pose a major risk if not stored properly.
Hot work operations like welding and cutting generate sparks that can ignite fires, especially in areas with flammable substances.
Fire Hazard | Cause | Prevention Measures |
---|---|---|
Electrical Faults | Overloaded circuits, faulty wiring, overheating machinery | Regular PAT testing, scheduled maintenance, proper wiring insulation |
Flammable Materials | Poor storage of chemicals, combustible dust accumulation | Proper ventilation, safe storage cabinets, regular housekeeping |
Hot Work Operations | Sparks from welding, cutting, and grinding near flammable substances | Designated safe work areas, fire-resistant barriers, hot work permits |
Blocked Fire Exits | Poor housekeeping, improper stock storage | Clear pathways, routine safety checks, staff training |
Lack of Fire Equipment | Non-functional alarms, expired extinguishers, no sprinklers | Regular inspections, staff fire extinguisher training, sprinkler installations |
In many cases, fires worsen due to inadequate fire safety equipment. Non-functional alarms, expired extinguishers, or the absence of sprinklers can allow a minor fire to grow out of control.
A notable example occurred in 2022 when a Birmingham plastics factory suffered extensive damage due to improper storage of flammable materials, highlighting the importance of strict fire safety compliance.
This incident also underscores the need for adherence to DSEAR (Dangerous Substances and Explosive Atmospheres Regulations) to properly manage and store hazardous substances, reducing the risk of fire and explosions. Read more about DSEAR here.
You may also like DSEAR Compliance For Corporate Entities
Conducting Fire Risk Assessments
Conducting fire risk assessments is a key part of ensuring workplace safety in your factory. This process involves identifying potential fire hazards and evaluating the risks associated with them.
Start by inspecting your premises thoroughly. Look for flammable materials, faulty equipment, or any other potential sources of ignition.
You should assess the likelihood of a fire occurring and the potential consequences if it does. Consider factors such as the layout of your factory, the presence of fire exits, and the accessibility of firefighting equipment. Document your findings, and don’t forget to include who might be at risk, such as employees and visitors.
Once you’ve completed your assessment, you need to prioritize the risks you’ve identified. Implement measures to minimize these risks, whether it’s improving ventilation, training staff on proper handling of flammable materials, or upgrading your fire detection systems.
Be sure to review and update your fire risk assessment on a regular basis, especially when there are changes in your factory layout or work processes.
Despite the critical importance of fire risk assessments, in the year ending March 2024, 42% of fire safety audits in non-domestic premises were deemed unsatisfactory Regular and thorough assessments allow you to identify and mitigate potential fire hazards effectively.
By staying proactive, you’ll create a safer environment for everyone involved.
Ensure your factory meets the highest fire safety standards: Book a professional fire risk assessment with our experts today.
Implementing Fire Safety Training
Fire safety training is not just a legal requirement for UK factories, it’s a critical measure to protect workers, machinery, and stock from devastating fire incidents.
Unlike office environments, factories contain high-risk equipment, hazardous materials, and complex layouts.
So while fire safety is crucial in any workplace, the scale and potential impact of a factory fire make rigorous fire prevention and training even more important.
Who Needs Fire Safety Training in a Factory?
Fire safety training should be provided to all employees, but certain roles require specialized instruction:
Factory Floor Workers
These employees operate machinery, handle flammable substances, and work in high-risk areas. They need basic fire safety training, covering how to identify fire hazards, operate extinguishers, and follow evacuation protocols.
Fire Marshals (or Wardens)
At least one designated fire marshal should be trained in advanced fire safety procedures, including fire risk assessments, emergency response coordination, and using firefighting equipment.
Warehouse & Storage Personnel
Employees working in stockrooms should receive fire load management training, focusing on safe storage practices for flammable materials and emergency response for warehouse fires.
Maintenance & Engineering Staff
Given their involvement with electrical systems and machinery, they should receive fire prevention and electrical fire safety training, helping them spot risks before they become hazards.
Supervisors & Managers
Factory leadership must understand fire safety compliance under UK law, ensuring proper procedures are enforced and audits are conducted.
FIRE STRATEGY – ARE YOU ACCOUNTABLE? SPEAK TO AN EXPERT
Recommended Fire Safety Training for Factories
To ensure compliance with the Regulatory Reform (Fire Safety) Order 2005, factories should consider the following UK-approved courses:
— Basic Fire Awareness Training
— Fire Marshal/Warden Training
— Hot Work Fire Safety Training
— Chemical & Flammable Substances Handling
— Fire Risk Assessment Training
Why Factories Need Extra Attention to Training
Factories differ from other workplaces due to their higher fire risk, faster fire spread, and greater potential for damage. The presence of heavy machinery, high-voltage electrical systems, flammable substances, and large-scale production processes means a small oversight can lead to catastrophic results.
A well-trained workforce is the first line of defense against fire incidents. When employees understand fire hazards, recognize early warning signs, and know exactly how to respond, they reduce risks, prevent escalation, and protect lives. Regular fire drills and ongoing refresher training ensure that fire safety remains a priority, rather than an afterthought.
By investing in proper fire safety training, UK factories can stay compliant, minimize risks, and safeguard their business from preventable disasters.
Provide refresher courses to keep safety practices top of mind.
Installing Fire Prevention & Suppression Systems
Consider installing automatic fire suppression systems, such as sprinklers or foam systems, that activate when a fire is detected. These systems can quickly control or extinguish a fire before it spreads.
Smoke detectors and fire alarms are key for early detection. Make sure they’re strategically placed throughout the facility and regularly tested.
Remember fire extinguishers. Position them in accessible locations, and train your staff on their proper use.
Installing an emergency lighting system will also guide employees safely during an evacuation.
UK factories often require additional levels of fire prevention measures due to the scale of operations and machinery involved.
You should therefore you should consider these additional fire suppression methods:
Fire Compartmentation
Heat and Smoke Ventilation
Automatic Fire Suppression Systems
Thermal Imaging Technology
Promoting a Safety Culture
A strong safety culture in your factory is important for creating an environment where everyone prioritizes fire safety.
When your employees feel responsible for safety, they’re more likely to engage in practices that prevent fires and protect their colleagues.
Here are some key strategies to help you promote this culture:
— Encourage Open Communication: Make it easy for employees to voice concerns and share suggestions about fire safety without fear of judgment.
— Provide Regular Training: Equip your team with knowledge and skills through ongoing fire safety training sessions, ensuring everyone knows how to respond in emergencies.
— Recognize Safe Behaviours: Celebrate individuals or teams that consistently demonstrate commitment to safety, reinforcing the importance of proactive fire prevention.
Conclusion
To improve fire safety in your factory, focus on compliance with the Regulatory Reform (Fire Safety) Order 2005. Focus on regular fire risk assessments and training, along with effective fire prevention systems.
You should also prioritize promoting a safety culture; encourage open communication and recognize safe practices among your team.
With these best practices, you’ll not only meet legal requirements but also create a safer work environment that protects everyone.
If you have any questions or would like to arrange a free consultation drop us a message here
My Fire Safety. Co-Space, 25 Town Square,
Stevenage, SG1 1BP. 0800 999 11 25
Related Fire Safety Training Courses:
Fire Risk Assessments
Evac Chair Training
Fire Marshal Training
Fire Alarm Training
Sorry, the comment form is closed at this time.